The Transformative Power of 3D Printing in the Collision Industry: Saving Cost and the Environment
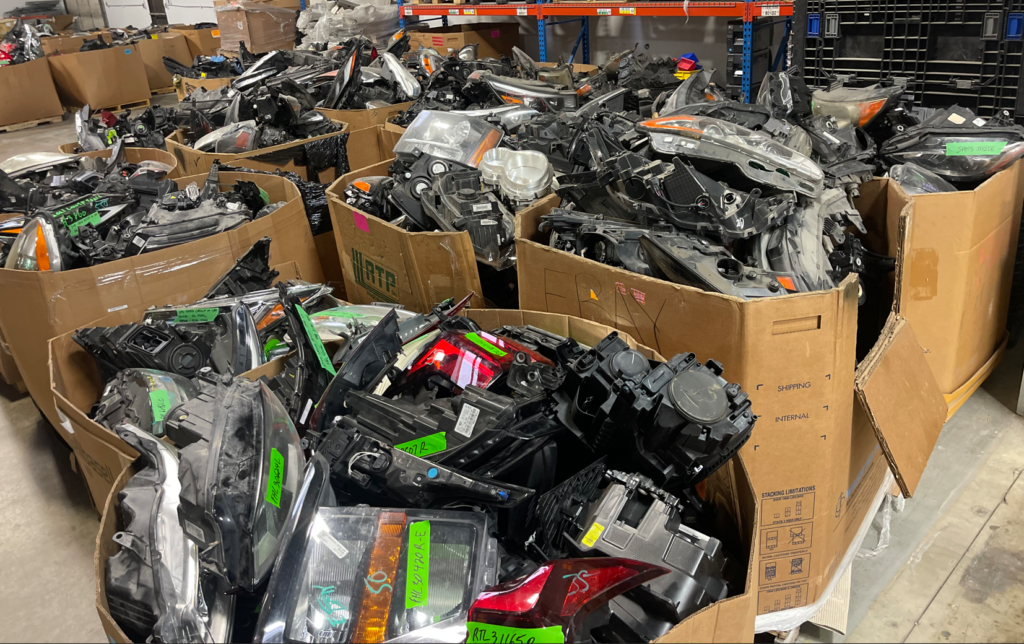
The collision industry is buzzing with excitement over the potential of 3D printing technology and advanced materials like polypropylene. One of the most impactful applications is repairing damaged parts, such as headlights, by printing and attaching missing base tabs using various methods. This innovation brings significant economic benefits to repair shops and insurers, while also positively impacting the environment.
Revolutionizing Headlight Repairs with 3D Printing
Traditionally, a broken headlight base tab meant replacing the entire unit. This replacement process involves high costs and logistical challenges, including manufacturing, storing, and shipping new parts. Headlight costs contribute significantly to rising repair expenses, which in turn drive up vehicle insurance premiums.
With 3D printing, high-quality, OEM-grade replacement tabs can be produced and welded onto existing headlights, restoring functionality and extending lifespan. This is particularly valuable in the collision industry, where even minor damages can lead to high repair costs. Utilizing 3D printing technology, repair shops can source replacement tabs on demand, reducing the need for extensive inventories and minimizing repair wait times. This enhances operational efficiency and reduces costs for both repair shops and customers.
Standardization and Testing
The collision industry has seen a rise in low-grade materials being used by some suppliers, leading to subpar repairs. It’s crucial for suppliers to use industry-ready, OEM-compatible parts and ensure transparency about the materials, testing, and printing technology they use. OEMs are adopting 3D printing for end-use parts, utilizing industry-grade machines for their manufacturing processes. Suppliers must use the same technologies to assure the industry that their parts are suitable and safe. Adhering to stringent standards and conducting rigorous testing guarantees that 3D printed parts meet or exceed the quality and safety benchmarks set by OEMs, fostering trust and reliability in the repair market.
Environmental Impact
3D printing in headlight repairs offers considerable environmental benefits. By avoiding the need to manufacture new parts, the industry can significantly reduce its carbon footprint. Traditional production involves substantial energy consumption and greenhouse gas emissions, from raw material extraction to manufacturing and transportation.
In contrast, 3D printing replacement tabs require significantly less energy. The process involves additive manufacturing using materials like polypropylene (PP), which can be done locally, reducing the need for transportation and storage. Additionally, 3D printing minimizes material waste, as parts are produced layer by layer using only the necessary amount of material.
Diverting Waste from Landfills
3D printing in the collision industry can also divert waste from landfills. Each headlight repaired instead of replaced saves about seven pounds of material from ending up in a landfill. Considering the millions of vehicles on the road and the frequency of headlight damage, this can significantly reduce automotive waste.
This reduction in waste has far-reaching implications. Landfills emit harmful gases like methane and contribute to soil and water contamination. By reducing the volume of waste that ends up in landfills, the collision industry can play a crucial role in mitigating these environmental impacts.
Economic and Operational Benefits
Beyond environmental benefits, 3D printing technology offers several economic and operational advantages for the collision industry. Producing replacement parts on demand can lead to substantial cost savings. Repair shops can reduce their dependence on external suppliers, minimize inventory costs, and avoid delays associated with ordering and shipping new parts.
Moreover, the flexibility of 3D printing allows suppliers to produce parts for a wide range of vehicle models and makes. This versatility is particularly valuable in an industry where parts compatibility can be a significant challenge. By having the capability to print custom parts as needed, repair shops can improve their service offerings and enhance customer satisfaction.
Future Outlook
The potential of 3D printing in the collision industry extends beyond headlight repairs. As technology continues to advance, a broader range of automotive parts will likely become suitable for 3D printing. This could further enhance the industry’s ability to repair rather than replace damaged components, leading to even greater environmental and economic benefits.
Additionally, the integration of 3D printing technology into the industry is driving innovation in other areas, such as custom parts manufacturing, rapid prototyping, and on-demand production of specialized tools and equipment. The flexibility and efficiency offered by 3D printing can drive significant improvements in the industry’s overall operational capabilities and have a huge impact on our environment by reducing the industry’s carbon footprint and diverting millions of plastic parts from landfills.